Prepreg Malzemeler Rehberi
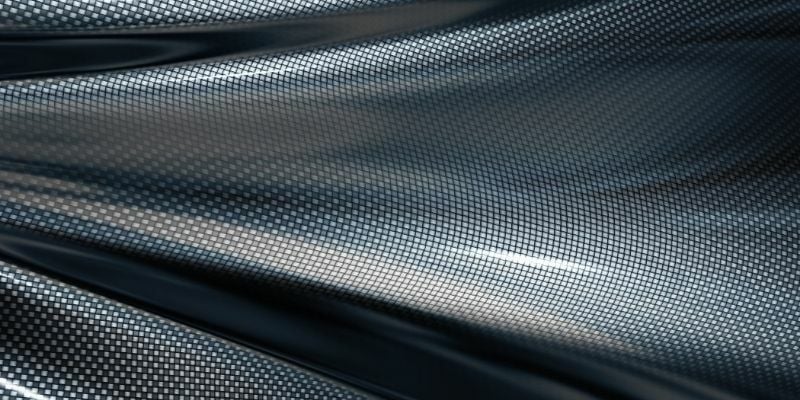
Prepreg malzeme kullanımı özellikle son zamanlarda kullanım kolaylığı ve yüksek kalite sunmasından dolayı gittikçe yaygınlaşmaktadır. Peki prepreg malzeme nedir? Bu ve daha fazlasına yanıt alacaksınız.
Prepreg Malzeme Nedir?
İlk önce prepreg malzemenin ne olduğunu anlamak gerekir. Prepreg malzeme, reçine ile önceden emprenye edilmiş bir takviye kumaşını tanımlamak için kullanılan genel bir terimdir. Bahsi geçen reçine genellikle epoksi reçinesidir. Ama termoset ve termoplastik reçineleri gibi farklı reçineler de kullanılabilir. Temelde termoset te termoplastik te bu malzemelerin arasında sayılır ama aralarında ciddi farklar bulunur.
Prepreg Malzeme Çeşitleri
Malzeme çeşitleri, termoplastik ve termoset olmak üzere ikiye ayrılır. Detaylıca inceleyelim:
1. Termoplastik
Termoplastik reçine kullanılarak önceden emprenye edilmiş kompozit takviyelere termoplastikprepreg denir. Cam elyafı, karbon fiber ve aramid bu takviyelere örnek gösterilebilir. Termoplastiklerde yaygın olarak kullanılan reçineler PP, PET, PE, PPS ve PEEK’dir. Tek yönlü batta, dokunmuş veya dikişmiş kumarlarda termoplastikprepreg kullanımı sağlanabilir.
2. Termoset
Termosetprepregler daha yaygın olarak kullanılır. Birincil olarak kullanılan reçine matrisi epoksidir. Bundan farklı olarak BMI ve fenolik reçineler de prepreg halinde yapılır.
İlk etapta termoset reçine ile termosetprepreg reçine sıvı olarak başlar ve lifi tamamen emprenye eder. Bu reçine sıvı, ısıyla sertleşmiş bir biçimdedir. Reçinenin fazlası ise takviyeden ayrılır. Bu sırada epoksi reçinenin bir kısmı kürlenmeye maruz kalır ve reçine sıvıdan katıya hal değiştirir. Bu durum "B” aşaması olarak adlandırılır.
B aşamasında kürlenen reçine genellikle yapışkan bir yapıya sahiptir. Reçine yüksek bir sıcaklığa getirildiği esnada sertleşmeye başlamadan önce genellikle kısa bir süre için sıvı duruma geri döner. Sertleşme tamamlandıktan sonra B aşamasındaki reçine artık çaprak bağlanmış durumdadır.
Termoset ve termoplastikpreparasındaki en temel fark, termoplastiklerin oda sıcaklığında olması ve raf ömrünün daha uzun olmasıdır. Bunun dışındaki farklar, bu en temel farkın doğurduğu sonuçlardır.
Prepreg Malzemelerin Avantajları
Prepreg malzemelerin birden fazla avantajı vardır. Bunları detaylı inceleyelim:
Maksimum Mukavemet Özellikleri: Genellikle el laminasyonunda, %50 reçine içeriği elde etmek güç bir durumdur. Bu da demek oluyor ki, laminat ağırlık %50 ve reçine oranı %50’dir. Standart el laminatları, vakumla torbalandığı halde dahi ciddi miktarda reçine reçine fazlası ile sonuçlanır. Bu durumda fazla reçine hem hassasiyeti arttırır hem de özelliklerini azaltır. Bunun yanı sıra prepreg bünyesinde genellikle %35 oranında reçine barındırır. Bu oran maksimum sertleşmeyi sağlamak için idealdir. Ayrıca bunu el laminasyonunda elde etmek neredeyse imkansız bir durumdur.
Parça Bütünlüğü ve Tekrarlanabilirlik: Reçine açısından zengin alanlar ve kuru noktalar, el laminasyonu tekniklerinin oyunları olmadan sağlanamaz. Hem teorik olarak kalıptan çıkan her parçanın aynı olması gibi bir olasılık söz konusudur hem de parçalar kalınlık açısından da aynılık gösterecektir. Tabi ki vakumlu torbalama teknikleri, taşıma gibi konularda bir hata payı her zaman mevcuttur. Ancak prepreg kullanımı, yaşanabilecek hata payını ciddi ölçüde azaltır.
Daha Az Karışıklık ve Daha Az Atık:Kürlenme işlemi esnasında prepregler fazla reçineyi takviyeden atar. Fakat el laminasyonunda tüm bu fazlalıklar (reçine kapları, dağınık silindirler, damlalar vs. gibi) bir sorun teşkil etmez. Prepreglerin oda sıcaklığında işlenmesi, zamandan tasarruf edilmesi açısından önemli bir faktördür.
Daha Az Sertleşme Süresi: Isıl kürlenme döngüsünün tamamlanmasıyla parça servise hazır demektir. Genellikle tipik bir el laminasyonu için kürleşmeden maksimum verimi alabilmek için standart olarak 48 saat beklemek gerekir. Fakat ısıl kürlenme ile bu süreyi beklemeye gerek kalmaz.
Daha İyi Kozmetikler:El laminasyonunda olduğu gibi kalıp hazırlama ve kalıptan ayırma hala önemli ve gereklidir. Ayrıca parçanın kozmetik özelliklerini direkt olarak etkiler. Hava kabarcıklarının ortadan kalkması, hem pürüzsüz hem de parlak bir yüzeye ulaşılmasında ciddi farklar yaratır.
Prepreg Malzemelerin Dezavantajları
Prepreg malzemelerin avantajları olduğu gibi doğal olarak bazı dezavantajları da mevcuttur. Daha detaylı inceleyelim:
Maliyet: Değinilmesi gereken ilk dezavantaj yüksek maliyetlere sahip olmasıdır. Bu süreçte kullanılan reçine, kür ve kumaş maliyetleri de dahil tüm bu malzeme maliyetleri hesaplandığında yine de prepreglerin maliyeti daha yüksektir.
Raf Ömrü: Yüksek sıcaklıklarda depolama yapmak veısı kürleri raf ömrünün azalmasına sebep olabilir. Malzemeyi soğuk tutmak ve dondurmak, bu problemin çözülmesinde ciddi yardımcı olabilir.
Gerekli Isı Kürü: Isı kaynağı ve vakumlu torbalama olması gereklidir. Bu sıcaklık hiç değilse 270 °F derecesinde olmalı ve dört saat kadar sürdürülebilmelidir. İmalatçılar genellikle otoklav kullanır. Fakat herhangi bir ıs kaynağı da aynı işlevi görecektir.
Prepreg Malzeme Nasıl Kullanılır?
İlk olarak kalıp hazırlanır. PVA ile kaplanmış bir kalıp kullanmak, parlak bir parça elde edebilmenin en temel yoludur. Kumaş kalıba yerleştirilmeden önce soyulması gereken iki arka tabaka arasında prepreg yerleştirilir. Malzeme yapışkan bir yüzeye sahip olduğunda kalıba yerleştirilirken dikkatli olunması gerekir. Kalıp ayrıcısı sabitlenmeden malzeme yeniden konumlandırılamaz. Ayırıcının yeniden konumlandırılmasıyla birlikte PVA yukarı çekilecektir. Bu kaymanın engellenmesi için su bazlı kalıp ayırıcılar kullanılabilir. Fakat bu daha mat ve pürüzlü sonuçlar elde edilmesine sebep olabilir. Çeyrek inç kalınlığa kadar katmanlar üst üste yerleştirilebilir.
Bu durumda prepreg B aşamasında kürlenmiş bir vaziyettedir. Makas veya bıçak yardımıyla şekillendirilebilir, işlenebilir ve kalıba sıkıca yerleşir. Yine de en nihayetinde düzeltme gerektiren kabartmalı kesimler veya pileler olabilir.
Bundan sonraki aşamada kalıba yerleştirilmiş olan malzeme arasındaki havayı çıkarmak ve fazla reçineyi sıkmak için kalıp sıkıştırılmalıdır. Aslına bakılırsa bu aşamada çok az bir reçine fazlası bulunur ama sıcaklığın yükselmesiyle beraber reçine incelir. Tamamen sertleşmeden önce reçine fazlası oluşur.
Reçine fazlasının akıtılması için pres kullanılarak sıkıştırma yapılabilir fakat pres kullanılabilmesi için parçanın tamamen düz olması gerekir.
Parçanın hazır hale gelmesi için en temel ihtiyaç zamandır. Ne kadar katman döşenirse, aralarında oluşacak hava olasılığı da artar. Vakum torbalama tekniğinin olabilecek en kusursuz hale getirmek, bu olasılığı azaltır. Hedef sıcaklığa ulaşmak için sıcaklık dakikada5°F’den fazla olmayacak oranda arttırılabilir. Sertleşme döngüsü boyunca sıcaklık korunmalı ve fırından çıkmadan sıcaklık 150 °F’ye getirilmelidir. Parça oda sıcaklığına geldikten sonra parça kalıptan çıkartılır.
Kullanılacak süre ve ısı miktarını belirlemede dikkat edilmesi gereken bazı noktalar vardır. İlk olarak gerekli zaman varsa parçayı ısıda bırakmak için 24 saatlik bir zaman kullanılmalıdır. Isıya az maruz kalması sorun teşkil etmezken çok kalması sorun yaratabilir.
İkinci olarak, sıcaklık ve kürleme döngüsünü belirlemede kalıbın kütlesi ve iletkenliği göz ardı edilmemelidir. Çünkü bu süreçte ısının iletilmesi belirleyici olacaktır.
Üçüncü olarak, kalıbın kalitesi, malzemesi ve sıcaklık kısıtlamaları etkileyici olacaktır. Parçanın ısıya maruz kalması deformeye sebep olabilir.